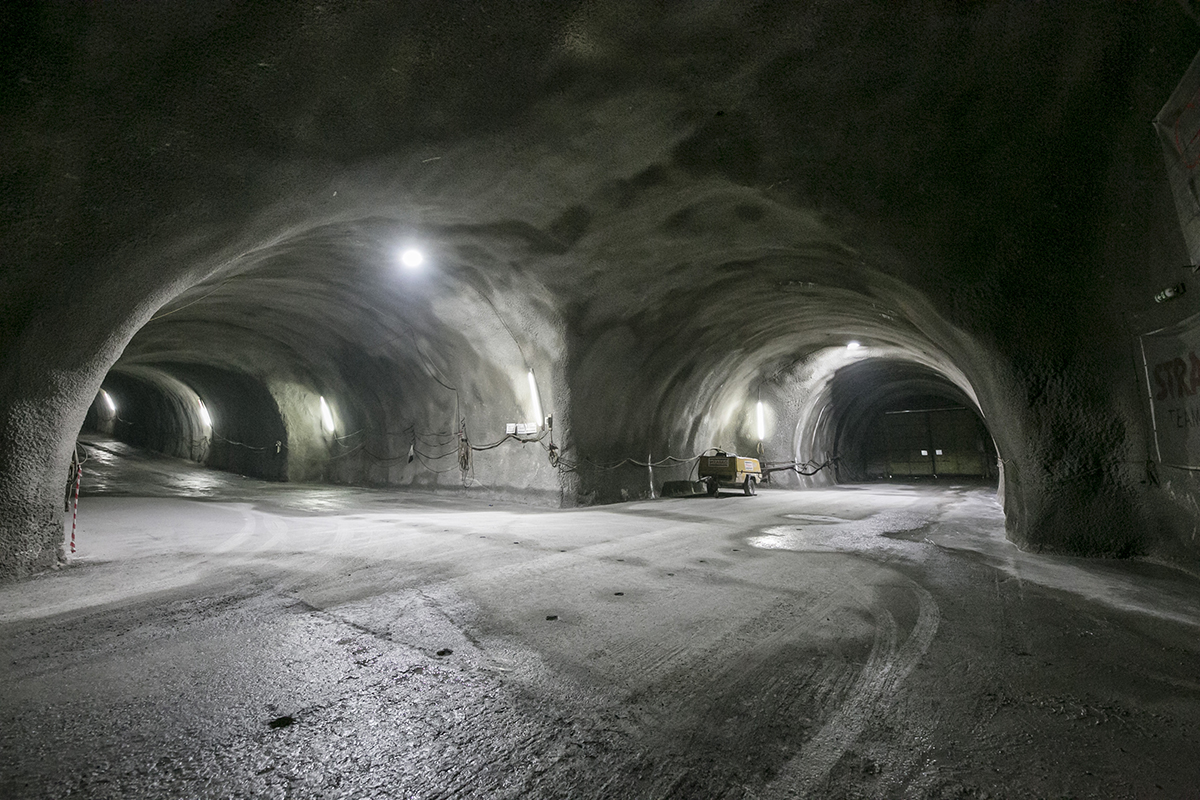
Europe is home to many rail, road, and canal tunnels. With rail travel being a greener mode of transport, the region will see more tunnelling projects come about in the next few years. Scottish manufacturer Terex Trucks explains why these undertakings require extra tough machinery and how its articulated haulers get the job done in these challenging working environments.
Across Europe, there are many exciting tunnelling projects ongoing. As part of the EU’s initiative for sustainable mobility, France and Italy are currently building a 57.5 km (36 mi) high-speed railway base tunnelunder the Alps between the cities of Turin and Lyon. This major infrastructure project is the latest addition to Trans-European Network (TEN-T) and will connect southwestern Europe with Central and Eastern European countries, aiming to shift freight trucks from Alpine roads to rail.
It’s no secret that to build such a tunnel, contractors require extremely robust and highly productive machinery. Terex Trucks’ articulated haulers, the TA300and TA400, are proven performers in the toughest applications. With its robust, reliable articulated haulers, Terex Trucks is ready for more tough tunnelling projects across Europe. But what makes these machines such a good fit?
- Maximum uptime for a 24-hour working schedule
Tunnelling is no nine-to-five job: the projects usually operate on a very tight schedule, which means the machines working in the tunnel have to follow an intense schedule and usually run around the clock, seven days a week. Any unscheduled downtime can cause delays and increases costs, so machine reliability and availability are important requirements.
To ensure maximum uptime, Terex Trucks uses a long-life transmission fluid that extends oil change intervals. The TA300 has a maintenance interval of 4,000 hours and the TA400’s transmission has an oil change interval of 6,000 hours. Terex Trucks has also extended the maintenance life of the actuation hydraulic fluid to 4,000 hours. This does not only increase uptime; the reduction in consumption and disposal of fluids also helps customers to minimise the environmental impact of their operations.
The machines’ magnetic suction filters further improve machine availability by reducing the risk of contaminants entering the hydraulic system. This keeps the hydraulic oil cleaner and prolongs hydraulic component lifecycles.
- Operational safety
With the TA300 and TA400’s exhaust brake, operators don’t need to use the brakes when driving down an incline in a tunnel. The machines’ modulating transmission retarder is coupled with an efficient exhaust brake and fully enclosed oil-cooled multidisc brakes, to provide high levels of machine control and operational safety.
When working in a tunnel, visibility is key. To ensure safe operations, Terex Trucks haulers are equipped with effective hazard area communications, including indicators for left and right as well as directional lights, often backed up by additional supporting lights. A cabin mounted flashing beacon provides a brighter light output even in harsh conditions, and the reverse audible alarm and flashing light warn anyone in the hauler’s path that it is moving backwards.
- Powered by strong and fuel-efficient engines
Excavating a tunnel creates tons of debris. To move the rocks out of the way, haulers sometimes have to drive for many kilometres to reach the end of the tunnel, going up and down inclines with their ton loads. This puts equipment to the test, and to deliver an efficient performance a powerful engine is key.
Thanks to a drivetrain that’s perfectly matched with the engine, Terex Trucks haulers deliver powerful performance and excel in demanding work environments. The TA300 and TA400 are both equipped with Scania engines. The TA300 is powered by a Scania DC9 engine, which develops gross power of 370 hp (276 kW) and a maximum torque of 1387 lbf ft (1880 Nm), and the TA400’s Scania DC13 engine develops gross power of 331 kW (444 hp) and a maximum torque of 2,255 Nm (1,663 lbf ft).
Both the TA300 and TA400 have recently been updated with an EU-Stage V emission-compliant engine and now boast a reduction in fuel consumption of up to 7% (compared to the Stage IV machines). This improvement is achieved with advanced engine control and effective fuel injections. In combination with its latest upgrade to a highly efficient 8-speed transmission, the Stage V TA300 even delivers fuel consumption savings of up to 10%.
The TA300 and TA400 come with three-stage aspirated air filtration, which provides increased engine protection to lengthen maintenance intervals. An effective power-to-weight ratio of the haulers ensures that material is moved as quickly as possible.
- A comfortable working environment
Working in a tunnel is not only challenging for machines, but it is also a tough environment for operators. That’s why Terex Trucks has improved operator comfort and upgraded the cabs of the TA300 and TA400 with a high-performance heating and air-conditioning system. The sealing elements have installed pressurised properties, which helps keep the in-cab temperature stable and minimizes particle ingress.
- Easy to maintain
For tunnel projects especially, the ease of maintenance matters when contractors choose a hauler. To increase the availability of machinery, servicing should be as easy and safe as possible. Both the TA300 and TA400 have a fully tilting cab for easy access, and the electronically raised hood allows technicians to reach the engine service points quickly. In addition, most maintenance can be conducted at ground level and there’s no need to remove multiple parts.
With the Terex Trucks Haul Track Telematics system, customers always know how their haulers are performing, which helps to better plan maintenance. If a machine is underperforming, customers will notice it, which means they can detect and investigate any issues quickly.
Currently, five Terex Trucks haulers are showcasing their powerful performance in Hong Kong’s biggest tunnel construction project, the Central Kowloon Route. Prominent French contractor Bouygues Travaux Publicschose twelve TA400 haulers for this demanding job and is impressed with the efficiency of the machines.
“At Terex Trucks, we have over 80 years’ experience in building tough, reliable off-highway haulers,” says Paul Douglas, managing director. “This strong hauling heritage is reflected in our products today. The TA300 and TA400 are straightforward machines that get the job done, no matter what.”